Products & Services
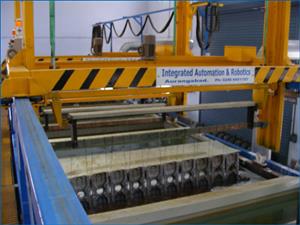
Phosphating Process Plants
Phosphate coatings are often used to provide corrosion resistance, however, phosphate coatings on their own do not provide this because the coating is porous. Therefore, oil or other sealers are used to achieve corrosion resistance. This coating is called a phosphate and oil (P&O) coating. Zinc and manganese coatings are used to help break in components subject to wear and help prevent galling.
Most phosphate coatings serve as a surface preparation for further coating and/or painting, a function it performs effectively with excellent adhesion and electric isolation. The porosity allows the additional materials to seep into the phosphate coating and become mechanically interlocked after drying. The dielectric nature will electrically isolate anodic and cathodic areas on the surface of the part, minimizing under film corrosion that sometimes occurs at the interface of the paint/coating and the substrate
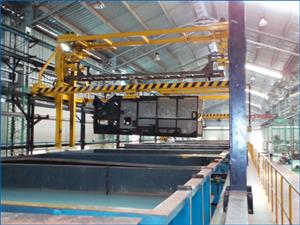
Pre Treatment Plants
A thorough material pretreatment is the fundamental prerequisite of any high quality coating. Wet or Dry pretreatment, depends on the material to be coated. Integrated Automation & Robotics provides solutions for degreasing, phosphating, grinding, shot blasting or ionizing on the turnkey basis with requisite Material Handling and Automation.
Integrated Automation & Robotics is the leading provider & specializes in manufacturing and exporting of Automatic Pretreatment Plants, which are admired by clients for their robust construction and automatic smooth functioning. These Pre treatment plants are fully programmed according to the process requirements of the client. Pretreatment Plants are used for surface preparation for painting, powder coating, ED coating etc. (This includes Cleaning and phosphating, Cromatising etc)
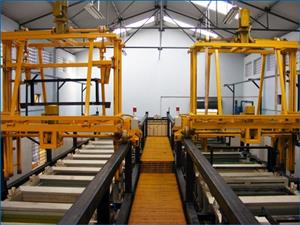
Zinc Plating Plants U Shape
Zinc Electroplating is one of the most common forms of electroplating and popular because of its relatively low cost, protective nature and attractive appearance. The coating done through this process gives corrosion protection to ferrous components and it can give colors like gold, black or olive drab finish, by post treatment.
The zinc electroplating process can be used to coat nuts, bolts, washers and automotive parts, such as interior components and gas filters. It also provides an effective undercoat for paints, when high corrosion performance is required. The most widely used zinc plating solutions are acid chloride, alkaline non cyanide, and cyanide, and the most widely used zinc alloys for electroplating are zinc-nickel, zinc-cobalt, and zinc-iron.
Any metal can be plated through the zinc electroplating process, but the most common are steel and iron, on which the process offers sacrificial protection.
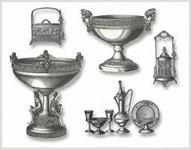
Silver Plating
Silver plating offers the following advantages :
Silver has highest electrical conductivity when compared to all other metals
Silver has high electrical and thermal conductivity
Silver is corrosion resistant
Silver has excellent solder ability
Despite being tarnished easily, silver can be cleaned and polished